Which sales region do you want to see the portfolio from? Our product range is not the same for every region. Therefore, make your choice here to see the right product range.
Extrusion and production of heavy filled PP
Our customer manufactures industry leading energy efficient components for glazing units. The process involves compounding and extruding PP heavily filled with glass fibre and desiccant.
The process resulted in high rates of premature wear to extruder and melt pump with a standard melt pump typically showing signs of wear at 6 months and housing falling out of specification around 12 months.
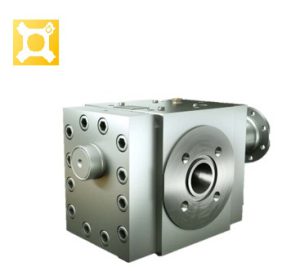
MAAG extrusion pump for boosting, type extrex GU-EP-EV
Why should you accept premature wear and tear?
For many years, the customer accepted premature wear as an inevitable consequence of their manufacturing process, however, Suurmond remained keen to investigate further prompting an 18 month study to determine root cause and any potential improvements.
Following consultation with our colleagues at MAAG, it was suspected the upgraded design features and volumetric efficiency of the ‘Generation 6 range’ could benefit this specific process and in 2020 we installed the first EX50-6 pump unit into the line and monitored closely.
Strong improvement leads to further upgrading of other lines
Over the following 12 months it became obvious previous issues experienced had been greatly reduced if not eliminated. The positive results prompted a further two lines to be upgraded immediately, an additional two lines upgraded the following year and in 2023 expansion saw a completely new line installed with an EX50-6 pump unit as standard.
Optimal Durability
Our customer is delighted to report several key benefits to their business:
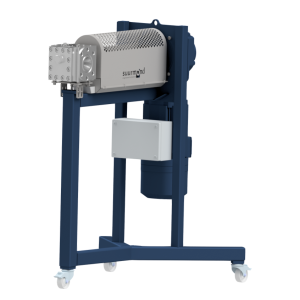
SUURMOND pump unit for a PP extrusion process
- reducing capital expenditure
- reducing downtime
- improving reliability
- improving dimensional stability
- improving product quality
Optimisation of silicone rubber production
The success of roll out prompted the client to approach Suurmond with an additional request to help reduce waste on a second core product comprising of Silicone Rubber.
Again, in consultation with MAAG, we supplied a MAAG EX56 RB melt pump running in conjunction with a Suurmond control system. In this case we significantly reduced waste, improved dimensional stability with added benefit of removing load and reducing wear on extruder components.
Don’t accept ‘what has always been done’
Within a busy manufacturing environment, it is often all too easy to repeat what has ‘always been done’. However, utilising Suurmond as a partner and sounding board in combination with the knowledge and experience of our key supplier partners we can help improve many processes. We look forward to discovering if we may be able to increase productivity, reliability and profitability on your specific application.
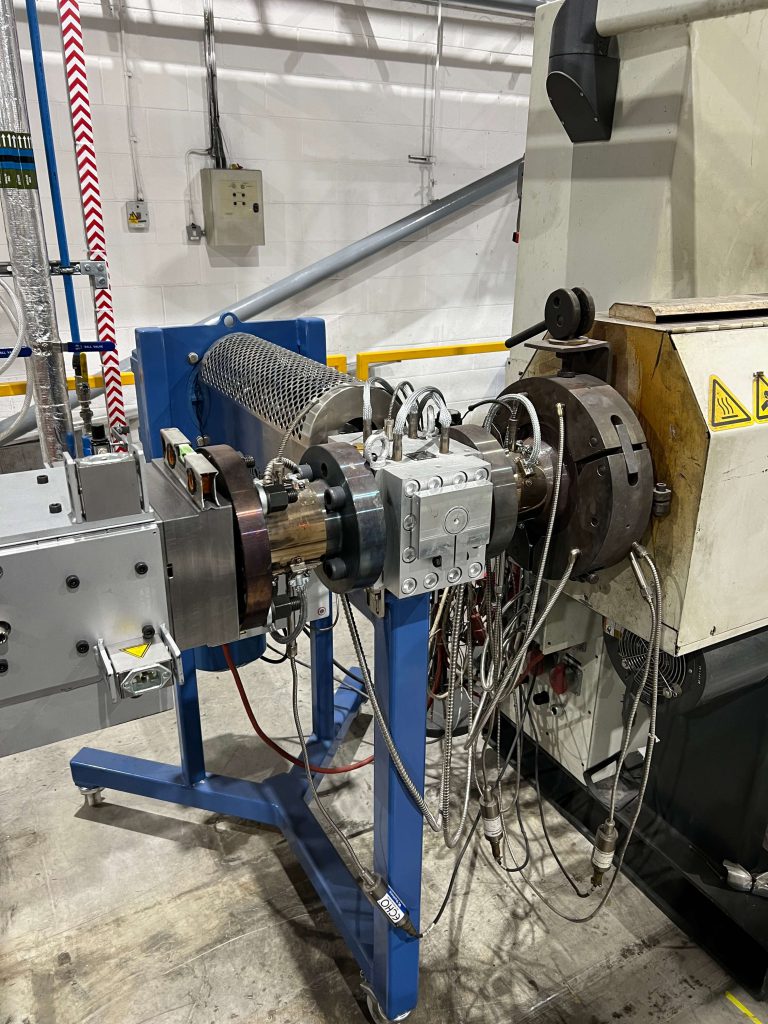
The SUURMOND pump unit for a PP extrusion process in production
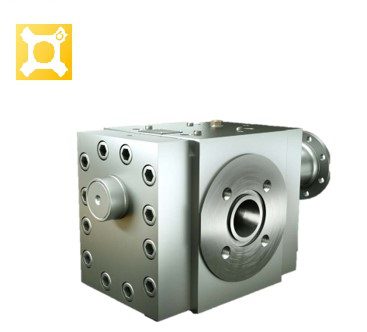
MAAG extrusion pump for boosting, type extrex GU-EP-EV
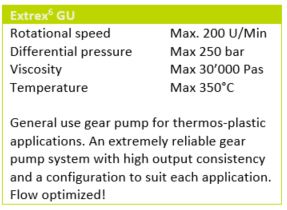
Table parameters MAAG extrusion pump type extrex6 GU
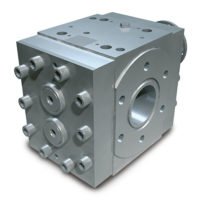
MAAG extrex RB melt pump, type extrex RB-RB
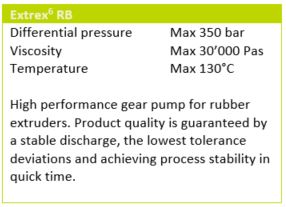
Parameters extrex RB melt gear pump for rubber extruders
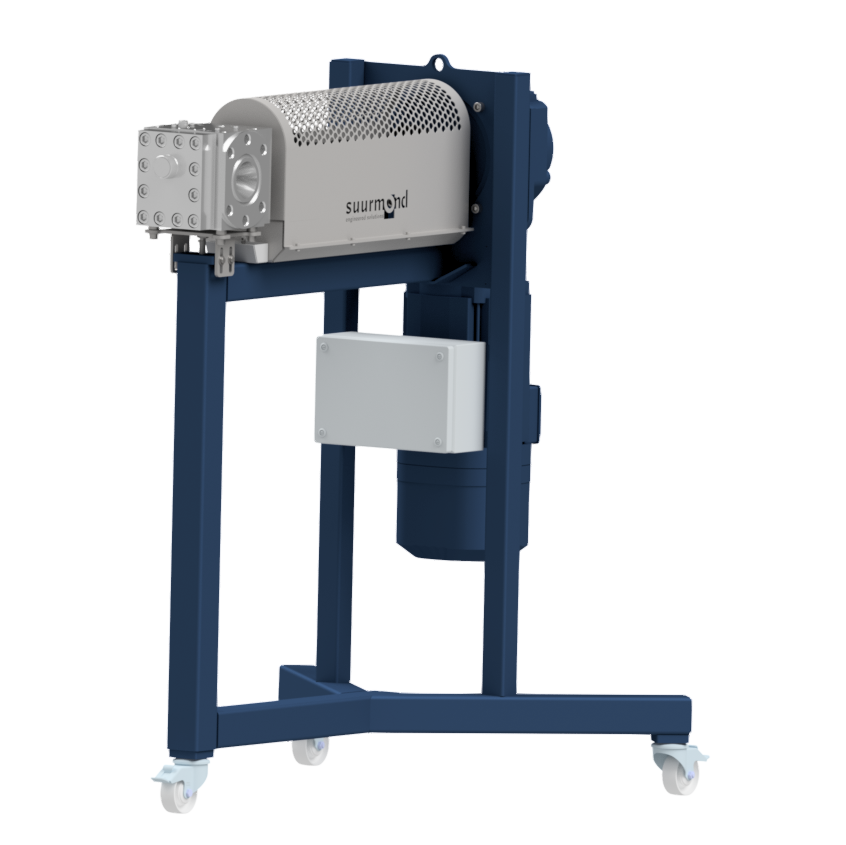
SUURMOND pump unit for a PP extrusion process